Review Paper
Electrocoagulation Process: A Mechanistic Review at the Dawn of its Modeling
Djamel Ghernaout1,2* Abdulaziz Alghamdi3 and Badiaa Ghernaout4
1Chemical Engineering Department, College of Engineering, University of Ha’il, Ha’il, Saudi Arabia
2Chemical Engineering Department, Faculty of Engineering, University of Blida, Blida, Algeria
3Mechanical Engineering Department, College of Engineering, University of Ha’il, Ha’il, Saudi Arabia
4Mechanical Engineering Department, College of Engineering, University of Amar Telidji, Laghouat, Algeria
*Corresponding author: Djamel Ghernaout, Chemical Engineering Department, College of Engineering, University of Ha’il, Ha’il, Saudi Arabia, Tel./Fax: +213-25-433-631; E-mail: djamel_andalus@hotmail.com
Citation: Ghernaout D (2019) Electrocoagulation Process: A Mechanistic Review at the Dawn of its Modeling. J Environ Sci Allied Res 2019: 22-38. doi: https://doi.org/10.29199/2637-7063/ESAR-201019
Received: 13 December, 2018; Accepted: 25 January, 2019; Published: 15 February, 2019
Abstract
During the two last decades, electrocoagulation method (EC) was the focus of many industrial applications and remains a fascinating domain of research. Most published researches concern uses in treating potable water and wastewaters to increase both the removal of dissolved and undissolved contamination. Significant achievements have been realized comprising participations to fundamental comprehension, electrode metals, working parameters, device conception, and economic aspects determinations. Despite the fact that there are several benefits mentioned through the specialized references, the EC large-scale use is not until now viewed as a recognized wastewater technique due to the absence of viable models used in designing device. The present review discusses the mechanisms involved in the EC process and opens a broad perspective on its modeling. The scientific community is near to suggest empirical/theoretical models to present the EC technology as a viable green process. However, more great efforts remain to be accomplished. Technological software developers such as COMSOL™ Multiphysics are invited to insert the EC process in their electrochemistry module to better commercialize this intensified technique and encourage its massive use through the world.
Keywords: COMSOL™; Electrocoagulation; Modeling; Potable water
Abbreviations
CCD: Central Composite Design
CFD: Computational Fluid Dynamic
EC: Electrocoagulation
FD: Factorial Design
RSM: Response Surface Methodology
Introduction
Preserving water resources becomes one of the humankind greatest challenges [1,2]. It has to treat many problems such as population growth, deforestation, rapid urbanization, industrialization and warming global climate change [3-5]. Now, the availability of potable water is restricted and not assured [6]; water contamination may significantly affect aquatic ecosystems and the accessibility to healthy freshwater [7]. Consequently, there is a necessity to promote performant techniques and methods for depolluting and controlling used waters [8], to preserving widely quality and increase quantity whereas assuring environmental safeguard [9,10]. At the same significance, more performant potable water processes treatment is needed to monitor hazards developed by ecological pollution [11-13]; as an illustration, existence of nitrate or fluoride ions at elevated levels [5,14].
The electrocoagulation (EC) technique may be employed for treating potable water and depolluting wastewater [15]. EC includes producing cationic metallic species inside the reactor through accelerated corrosion of consumable metallic anode induced via electric power exercised over the plaques [16]. Following the water acidity, the metallic cations formed electrochemically are instantaneously subjected to aquatic hydrolysis, producing different metallic forms comprising hydroxide flocs (eliminating contaminants through adsorption/settling). Usually, aluminum and iron metals are employed as electrodes due to several benefits: they are abundantly available at low cost, their relative low poisoning effect, and their elevated (+2/3 and +3, respectively) valence that conducts to a performant elimination of contaminant [17-19]. Moreover, concurrent cathodic reaction lets contaminant elimination either upon attachment on cathode or through fixation on H2(g) bubbles liberated at the negative pole. In a general manner, the anode and the cathode materials are selected from the identical metal, even if electrochemical dissolution should happen exclusively at the positive pole.
Usually, electrochemical coagulation is performed in two configurations: a batch or uninterrupted mode [20]. There is a vast number of cases where EC was successfully applied [21,22]. Relatively, EC is an ancient technique, at the same age as electricity [22]. Employing this electrochemistry-based method in treating potable water factories was mentioned during the 19th century in UK, and treating wastewater factories [23] in the United States in the dawn of the 20th [24]. In the late 30s, this electrical process has been substituted by conventional coagulation [25,26] and by biological techniques for eliminating colloids and dissolved organic matters in wastewater, respectively [27]. This was due to the more elevated functioning price; indeed, the cost of electricity at this time was insupportable. Naturally, the trend has radically varied, and the benefits of EC have been shown once again from the 80s. Several advantages have been mentioned in the written works [28] with the particular disadvantages of EC comparatively with competitive techniques, as listed in (Table 1). However, EC is known for additional problems than those mentioned in Table 1. As an example, the requirement for sludge treatment, even if conventional coagulation [29] and activated sludge method have to resolve the identical problem, remains to be resolved. The constitution of EC sludge is similar to that formed employing conventional coagulation [30,31] when either Al2(SO4)3.18H2O or FeCl3 are injected; this significates that sludge handling must be identical. On the contrary, a particular problem of EC is that, until recently, there are approximately no detailed surveys of EC modeling for treating water [5].
Benefits
|
Disadvantages
|
General technique
|
Requires repair
|
Treats potable water and used water
|
Electrode passivation over time [5]
|
Integrates oxidation, coagulation, and precipitation
(conducting to minimal capital costs [28])
|
The necessity of high-conductivity water
|
Decreased requirement for chemicals (substituted with metal electrodes and electric power) [32]
|
Lack of systematic reactor design [24]
|
Reduced operating expense
|
|
The decreased hazard of ancillary contamination
|
|
Minimal sludge formation
|
|
Without moving parts [5]
|
|
Reduced power needs
|
|
Solar energy may be employed [33]
|
|
Table 1: Benefits and disadvantages of the EC process [5,28].
|
Consequently, this work aims to abridge, debate, and examine breakthroughs on modeling methods realized for simulating the scaling-up the EC process. First, different mechanisms for contamination reduction are presented. After that, the fundamental process variables and device conception characteristics will be reviewed intending to initiating the specifics of modeling features. Subsequently, the principal techniques and design approaches will be assessed and associated with the techno-economic study of the EC method. Ultimately, several views for subsequent investigation and progress will be proposed.
Hypothetical Context of EC Technique
EC merges distinct mechanisms that may be electrochemical (metal dissolution and water reduction, pollutant electrooxidation or electro-reduction, etc.), chemical (acid/base equilibria with varying pH, hydroxide precipitation, a redox reaction in the solution, etc.) and physical (physical adsorption, coagulation, flotation, etc.) [34,35]. All the mentioned stages may happen successively or in parallel (Figure 1). Figure 1 focuses on the intricacy and the interaction among the routes of the electrochemical method. These routes are described in the following section [5].
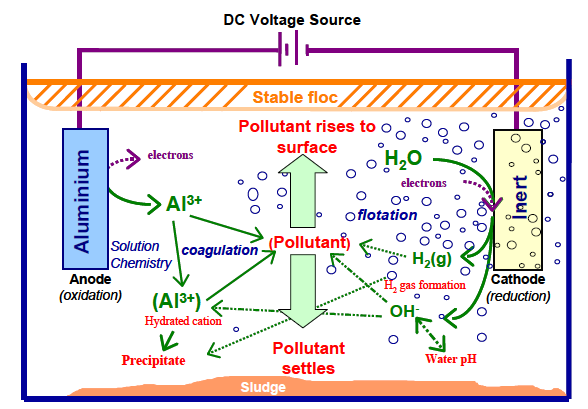
Figure 1: Mutual actions happening inside the EC device [36].
|
EC reactions
During the electrochemical coagulation technique, metal species are formed inside the recipient through dissolving electrochemically the metallic plaque, frequently in Fe or Al [5].
The involved reactions may be outlined:
- At the anode, the metal is oxidized into cations:
M → MZ+ + Ze- (1)
In Equation (1), Z is the number of electrons carried during the anodic dissolution phenomenon per mole of metal. In the situation of an elevated anode potential, there is a great probability that auxiliary reactions may happen [37,38]. Moreover, oxidation of water may conduct to hydronium cation and oxygen gas; in addition, if the chloride anions are present, they may be oxidized into Cl2. The last-mentioned being a powerful oxidant can take part in oxidizing the soluble organic matters or can conduct to generating ClOH that as well functions as an oxidizer [5,39].
2H2O → O2 + 4H+ + 4e- (E° = 1.23 V/ENH) (2)
2Cl-→Cl2+2e-(E°=1.36 V/ENH) (3)
Cl2+H2O→ClOH+Cl-+H+ (4)
- At the cathode: water is reduced into hydrogen gas and hydroxyl anions:
3H2O+3e-→(3/2)H2+ 3OH- (E° = 0.00 V/ENH) (5)
The quantity of metal solubilized through oxidization at the anode may be computed employing Faraday's law (Equation 6). Consequently, the amount of metal m depends on the residence period t and the electric current I [5]:
(6)
In Equation (6), M is the atomic weight of the electrode metal, and F is Faraday's constant. Nevertheless, Faraday's law Ø=1) is correct if all the electrons in the reactor take part exclusively in the metal-liberation phenomenon at the anode. In the case of parallel reactions happening, a corrective term, designated current efficiency or faradic yield (Ø), is employed to take into consideration the difference among the theoretical and experimental solubilization of the anode [40,41]. Generally, this term is smaller than 1 [42]; however, Ø may be bigger than one if the chemical and the electrochemical oxidation routes of the metal happen concurrently. This final case is recurrent with Al [43,44]. The metal cations liberated inside the solution go through diverse equilibrium reactions that correspond to the acid/base, complexation, precipitation and redox reactions. The contribution of these elimination routes is a function of pollutant species (Table 2) [5].
Dissolved contaminants
|
Removal mechanism
|
References
|
Sulfide anions
|
Precipitation
|
[45]
|
Calcium cations
|
Co-precipitation
|
[46]
|
Phosphate anions
|
Precipitation, adsorption, complexation
|
[47,48]
|
Organic compounds
|
Complexation, co-precipitation
|
[49,50]
|
Fluoride anions
|
Complexation, precipitation
|
[41,51]
|
Arsenate anions
|
|
[52]
|
Table 2: Equilibrium reactions of metal hydroxides with dissolved contaminants in the solution [5].
|
Nevertheless, concerning the positive ions liberated from the positive pole, the frequent event is the generation of Fe(OH)3(s)/Al(OH)3(s) that show low solubility and easily settle. Consequently, dissolved contaminants in water can as well be attached by physical or chemical means onto the flocs. Possible contamination removal routes implicate [5]:
- The completely physical entrapment of soluble matters happens through Fe(OH)3(s)/Al(OH)3(s), adsorption, and complexation. As an example, phosphates are eliminated upon complexing and/or by precipitating with Fe(OH)3(s)/Al(OH)3(s) and/or by attachment on the latter. At the same time, the soluble organic matter reduction may be explained by the co-precipitation and/or to complexation and/or to the electrostatic attraction on the surface of Fe(OH)3(s)/Al(OH)3(s). Concerning the complexation, the contaminant may play the role of a ligand (L) to fix a hydrous iron moiety or Al(OH)3(s) (Equations (7) and (8)):
L-H(aq)+(OH)OFe(s)→L-OFe(s) + H2O (7)
L-H(aq) + (OH)(OH)2Al(s) → L-(OH)2Al(s) + H2O (8)
- Electro-oxidating anodically or electro-reducing cathodically electro-active ions or molecules, like reducing Cr (VI) into Cr (III) may be followed by: (1) Cr (III) hydroxide settling [53], (2) reducing anionic nitrates into nitrite, (3) ammonia and nitrogen gas [54], and (4) oxidizing instead reducing if arsenic As (III) is oxidized into arsenic As(V) [55]. It was mentioned that heavy metals could as well go through electro-reducing cathodically throughout the electrochemical coagulation operation [56,57].
- Adsorbing directly contaminants on the electrodes surfaces: particularly for F- because of the electro-condensation where F- are fixed anodically upon the electric effects [58,59].
These pathways for dissolved contaminants are shown in (Figure 2). Practically, there is frequently a dominant mechanism for each pollutant depending on the type of this contaminant [5]. Frequent cases are listed in Table 2, and more information may be noted in survey articles on EC [22,54].
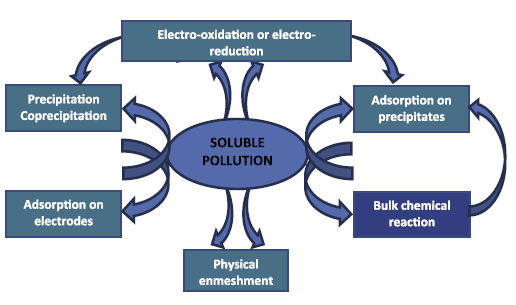
Figure 2: Principal mechanisms of dissolved contamination removal throughout EC [5].
|
Simultaneously, colloids and emulsions are as well neutralized through injecting coagulant without interruption from electro-dissolution like the conventional coagulation [60]. The penchant of colloids to destabilize or to persist distinctly and scattered is a consequence of the net inter-particles force that is envisaged upon the addition of opposing forces among the attractive van der Waals and the repulsive forces of the electrical double-layer as described by the DLVO [61,62] theory as a first approximation [63]. Neutralizing routes are listed in Table 3 [5].
Mechanism
|
Description
|
Compression of the double layer
|
The compression of the double layer of a colloid is formed by mutual actions with the soluble ionic species produced from the electrochemical dissolution of the sacrificial anodes. This compression impacts the electrical potential disparity among the particle surface and the bulk solution and conducts to decreasing the repulsive forces among particles [49].
|
Charge neutralization
|
Charge neutralization is realized through adsorption of ionic metal species/hydronium cations/hydroxyl anions or by the precipitation of charged hydroxide precipitates onto the surface of charged colloids existent in water/wastewater [64]. This charge neutralization may be illustrated through a variation of the zeta potential throughout the isoelectric point.
|
Sweep coagulation
|
Colloids entrapment (enmeshment mechanism or sweep coagulation): Hydroxide precipitates entrap the colloids existing in water/wastewater. This destabilization mechanism is a function of metal hydroxide precipitates that may be generated [64]. This mechanism dominates around pH 7 [65].
|
Table 3: Destabilization mechanisms of colloidal particles [5].
|
During the EC operation, these neutralization routes (Figure 3) can happen together or one by one following the characteristics of the water/wastewater to remedy, the contaminants to be eliminated, the working situations (particularly electric current), and the type of the metal. Opposite to dissolved contaminants, the controlling pathway is, consequently, more laborious to describe since it is frequently more related to working situations than on the type of the colloids. Then, the neutralization stage is pursued by flocculation that is composed of the assemblage of the destabilized colloids and the precipitates [66,67]. Flocculation performance is a function of the efficiency of the destabilization step and the collision velocity of colloids [5,49].
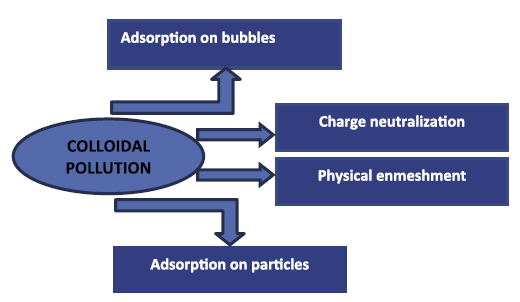
Figure 3: Principal mechanisms of insoluble colloidal contamination reduction employing EC [5].
|
Since reducing dissolved matters implicates attachment and entrapment, the routes of dissolved and solid matters are in themselves related. The aggregated pollutants, constituting EC sludge, may thus be eliminated physically from water, in the device or employing a downstream process (Figure 4). In the recepient, the two principal means implicate electroflotation (EF) and decantation [68,69]. Moreover, decantation and EF may as well be employed as downstream processes; however, in this situation, additional downstream techniques are accessible for sludge elimination comprising filtration, centrifugation, hydrocycloning, and flotation [5].
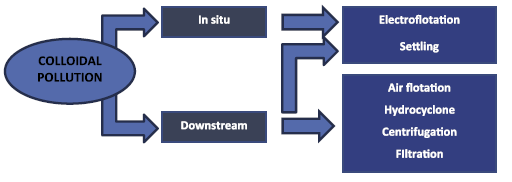
Figure 4: Principal mechanisms of EC sludge elimination [5].
|
Case of Al electrodes
For Al electrodes, only just the half-oxidation reaction among Al3+/Al pursues Equation (1), because Z = 3. More than the chemical equations presented above, additional monomeric species are produced from the instantaneous hydrolysis of Al3+ cations following the acid/base reactions (Equations (9)-(12)) and Al3+ amount [5,38].
Al3++H2O→Al(OH)2++ H+ (9)
Al(OH)2+ + H2O → Al(OH)2+ + H+ (10)
Al(OH)2+ + H2O → Al(OH)3 + H+ (11)
Al(OH)3 + H2O → Al(OH)4- + H+ (12)
Aluminum speciation and partition may be drawn from E-pH Pourbaix diagrams if the implied reactions are under thermodynamic control. This may be concluded from the equilibrium constants for acid/base reactions and standard reduction potentials listed in Table 4 [5].
Reaction
|
pK
|
Al3+ + H2O = Al(OH)2+ + H+
|
4.997
|
Al3+ + 2H2O = Al(OH)2+ + 2H+
|
10.094
|
Al3+ + 3H2O = Al(OH)3(aq) + 3H+
|
16.791
|
Al3+ + 3H2O = Al(OH)3(s) + 3H+ (amorphous)
|
8.578
|
Al3+ + 2H2O = AlO(OH)(s) + 3H+ (boehmite)
|
10.800
|
Al3+ + 4H2O = Al(OH)4- + 4H+
|
22.688
|
Reaction
|
E° (V)
|
Al3+ +3e- = Al(s)
|
-0.41
|
Table 4: Equilibrium constant (pK) and standard reduction potential aluminum species (E° (V)) of Al and Fe species [5].
|
Practically, dissolved Al3+ cations dominate if pH is less high than 4; dissolved aluminate anions take over if pH is more significant than 10, during the time that the insoluble Al(OH)3(s) form takes control apart from that [5].
The production of polymeric species has as well been mentioned: Al(OH)153+, Al7(OH)174+, Al8(OH)204+ and Al13O4(OH)247+ [5]. The Lewis acidity of aluminum equilibrates the generation of OH– anions at the cathode, which produces a buffered impact and conducts to a final pH among 7 and 8 which powerfully changes from conventional coagulation employing Al salts [49]. Therefore, monomeric and polymeric species provoke lately the production of the amorphous Al(OH)3(s) “sweep flocs” which possess important surface areas useful for fast adsorbing dissolved organic matters and trapping colloids [70-73]:
nAl(OH)3 → Aln(OH)3n (13)
Auxiliary reactions can happen on the electrodes because of a simple chemical attack of aluminum under acid or alkaline conditions, respectively [8,37]:
2Al + 6H+ → 2Al3+ + 3H2 (14)
2Al + 6H2O + 2OH- → 2Al(OH)4- + 3H2 (15)
The result is that the quantity of soluble Al liberated through the EC process overpasses the expected level predicted using Faraday's law [5]. Consequently, the faradic yield φ is more important than 100% and may attain 200% [38].
A problematic issue of EC technique is the passivation of the cathode since it elevates both the cell voltage and the energy consumption. The passivation phenomenon may be surmounted through optimizing the current reversal frequency [74] or NaCl injection to accelerate pitting corrosion upon a chemical reaction between Cl- fixed on the aluminum oxide film with Al3+ species in the oxide lattice [5]. The velocity of chemical corrosion of dissolved Al electrodes is a function of two mechanisms [75]:
• The generation and construction of a passive aluminum-oxide film;
• The following partial demolition of this film by pitting.
The pitting corrosion is a function of the initial pH, the type and the amount of supporting electrolyte [76] and the current density [5]. The favorable action of anions on passive aluminum-oxide film in the decreasing classification [77] is Cl-, Br-, I-, F-, ClO4-, OH-, SO42-. The pitting corrosion may significantly influence the global dissolution of sacrificial Al anode. The pitting potential Epit (V) diminishes with the logarithm of chloride concentration (ppm), as illustrated through Equation (16) [38]:
Epit=1.75-0.72×Ln[Cl- ] (16)
The pathway of chemical dissolution involved through pitting corrosion in the existence of chloride ions may be described [78]:
2Al + 6HCl → 2AlCl3 + 3H2 (17)
AlCl3 + 3H2O → Al(OH)3 +3HCl (18)
Case of Fe electrodes
The electrochemical reactions happening at Fe electrodes or in aqueous medium through Fe-EC are more complicated than with Al, because anode oxidation may conduct either to ferrous or ferric cations [5,79,80]:
Fe → Fe2+ + 2e- (19)
Fe → Fe3+ + 3e- (20)
Fe2+ and Fe3+ may be hydrolyzed in the recipient. Moreover, they may generate several monomeric and polymeric species whose proportions are function of the Fe3+ level and the pH degree: Fe(OH)2+, Fe(OH)2+, Fe(OH)24+, Fe(OH)4-, Fe(H2O)5(OH)2+, Fe(H2O)4(OH)2+, Fe(H2O)8(OH)24+, Fe2(H2O)6(OH)42+ and Fe(OH)3. This difficulty is as well illustrated in Table 5 that sums up the acid/base and equilibrium constants and standard reduction potentials of monomeric species [5].
Reaction
|
pK
|
Fe2+ + H2O = Fe(OH)+ + H+
|
9.397
|
Fe2+ + 2H2O = Fe(OH)2 + 2H+
|
20.494
|
Fe2+ + 2H2O = Fe(OH)2(s) + 2H+
|
13.564
|
Fe2+ + 2H2O = Fe(OH)3- + 2H+
|
28.991
|
Fe3+ + H2O = Fe(OH)2+ + H+
|
2.187
|
Fe3+ + 2H2O = Fe(OH)+ + 2H+
|
4.594
|
Fe3+ + 3H2O = Fe(OH)3 + 3H+
|
12.56
|
Fe2+ + 2Fe3+ + 8H2O = Fe3(OH)8(s) + 8H+
|
20.222
|
Fe3+ + 2H2O = αFeO(OH)(s) + 3H+
|
0.491
|
Fe3+ + 2H2O = γFeO(OH)(s) + 3H+
|
1.371
|
Fe3+ + 4H2O = Fe(OH)4- + 4H+
|
21.588
|
2Fe3+ + 2H2O = Fe2(OH)24+ + 2H+
|
13.771
|
2Fe3+ + 4H2O = Fe3(OH)45+ + 4H+
|
6.228
|
Reaction
|
E° (V)
|
Fe2+ + 2e- = Fe(s)
|
-0.41
|
Fe3+ + 3e- = Fe(s)
|
-0.04
|
Fe3+ + 2e- = Fe2+
|
+0.77
|
FeO42- + 3e- + 8H+ = Fe3+ + 4H2O
|
+2.20
|
Table 5: Equilibrium constant and standard reduction potential of iron species [5].
|
In spite of certain confusion in large part of the literature about the implied stages of Fe-EC, contemporary references largely hypothesis that the anode oxidation liberates Fe2+ since it has been established that the dissolution proportion of Fe3+ may be neglected [81-83]. The oxidation of Fe2+ to Fe3+ is a function of pH and the dissolved oxygen amount [84]. When pH is acid, ferrous cations oxidize very slowly in the presence of dissolved O2 (Equation (21)); however, if pH is neutral or alkaline, ferrous cations are instantaneously converted into Fe(OH)2 (Equation (22)) which is immediately oxidized by dissolved O2 to Fe(OH)3 (Eq. (23)) [5]:
Fe2+ + O2 + 2H2O → Fe3+ + 4OH- (21)
Fe2+ + 2OH- → Fe(OH)2 (22)
4Fe(OH)2 + O2 + 2H2O → 4Fe(OH)3 (23)
As a result, several references mentioned that the Fe dissolution obeys to the Faraday's law with a faradic yield comprised in the range of 80 and 100% [42,43,75]. However, different authors affirm that there is a gap between the quantity of Fe theoretically solubilized evaluated using Faraday's law and the quantity of detected solubilized Fe founded on Z = 2 [5]. If pH is acid, Ø is bigger than 100%; at the same time, if pH alkaline, the opposite is correct. At smaller pH degrees, acceptable interpretations are identical to those mentioned for aluminum: chemical corrosion and pitting corrosion at both electrodes in the existence of certain ionic species, like Cl- [5,75]. At bigger pH degrees, the dissolution efficiency diminishes under the Faraday's law levels since additional reactions happen next to the anode, comprising oxygen formation (Equation (2)). If pH is alkaline, Fe oxidation conducts to Fe(III) production following Equation (20) in the form of oxide or hydroxide species. This oxidation reduces the Fe amount generated since Fe(III) production needs 3 electrons instead of 2 for Fe(II) and consequently, a more important current level for attaining the equal Fe amount is necessitated [5,81]. The several monomeric and polymeric compounds ultimately convert into amorphous Fe(OH)3 flocss that are performant in quick adsorption of dissolved organic matters and enmeshing of colloids [85,86].
Moreover, there are two additional dissimilarities with aluminum electrodes: (1) the buffering impact mentioned for iron is less significant than for aluminum. Ultimate pH frequently attained is ~9-10 with iron electrodes even though pH is acid [84,87]. (2) Fe2+ is greatly dissolvable and thus not able of a performant colloidal particles destabilization upon Fe(OH)3, consequently inducing low EC efficiency [42]. As a result, a performant action of Fe-EC necessitates one or more of the next optimization methods for the Fe3+ formation [5,84]:
- Aerating the water to augment the solubilized O2 amount and Fe2+ oxidation;
- Augmenting the pH level to 7.5 or bigger to encourage the Fe2+ oxidation velocity;
- Adding oxidant like Cl2 that may be formed upon oxidization of the Cl- existent in the water on the Fe anode [5]. Thus, ferrous oxidation happens in the bulk solution, following:
Cl2 + H2O → ClOH + Cl- + H+ (24)
2Fe2+ + 2HOCl → 2Fe3+ + 2OH- + Cl2 (25)
Considering the electric current consumed through Cl- oxidation, this method is not performant unless the water/wastewater to purify holds more than 600 mg Cl-/L.
- Elevating the operation period to attain total ferrous oxidation.
Fe shows as well two extra benefits than Al: Fe is not poisonous; therefore, it may be employed for drinking water. The second one is the smaller cost of Fe, about 0.5-0.8 US$/kg, while Al cost is comprised between 1.5 and 3 US$/kg [5].
Fundamental Factors Affecting the EC Efficiency
The factors influencing EC performance are linked to (1) the working situations like current or voltage and residence period, to (2) water characteristics like pH, alkalinity and conductivity and (3) configuration of the EC device and its electrodes (electrode surface area, electrode inter-distance) [5].
Impact of the electric current
The electric current I is the most important parameter of EC. Practically, EC depends on the current density i that is described as the ratio of electric current over electrode surface area S. The continuity equation implies current conservation amongst the anode and the cathode; in fact, the current density may vary amongst the electrodes [5]:
I=iA×SA=iC×SC (26)
Current density dictates the coagulant injection from the anode and the hydrogen gas (H2) production from the cathode following the Faraday's law [5]. The bubble intensity influences the device hydrodynamics, which in turn affects mass transfer among contaminants, coagulant and gas micro-bubbles, and ultimately imposes collision significance of destabilized colloids and dissolved matters that conducts to flocs production [88]. Moreover, current density influences metal species during pH variation through EC operation in the form of a function of water alkalinity. As a result, the current seems to form a dynamic physical/chemical medium that dictates the coagulation/flocculation stages [89] and encourages the electromigration of ions and charged colloidal particles [18].
Cell voltage is linked in the form of equilibrium potential, anode and cathode overpotential as described through Eq. (35). Thus, electric energy consumption may be formulated in the form of contact period t employing [5]:
(27)
Since the electric energy needed for the EC method is related to the electric current and potential as described in Equation (27), EC may be performed either upon the (1) galvanostatic or (2) potentiostatic mode. For the first one, EC technique is realized through monitoring and/or modifying the current imposed over electrodes; at the same time, for the second one, it is the imposed cell voltage that is monitored and/or changed in the form of quantity of coagulant needed to be liberated in the EC device [5]. The second mode is not frequently employed for EC [90] and usually used for different electrochemical techniques like electro-oxidation and electro-reduction where sacrificial anodes are not employed [91,92].
Nevertheless, too high current amounts cam badly influences the EC performance. As an example, additional reactions can happen mainly, and overdosing may reverse the charge of the colloidal particles and disperse them another time conducting consequently to a diminution of the coagulant performance and a decrease of the anode lifetime [5].
The levels of the current density may largely change following the characteristics and the concentration of contaminants to be eliminated from water; as an example, from 0.01 A/m2 to 880 A/m2. Optimum current density must be evaluated following additional working indicators. To employ the EC reactor during a large time without stopping for maintenance, the current density is proposed to be among 20 and 25 A/m2 [77]. Moreover, high current augments voltage and ohmic drop among anode and cathode. Ohmic drop or IR drop is a consequence of the ohmic resistance of the electrolyte R, which may be described as follows [5]:
(28)
here d designates the inter-electrode gap, and k the water electric conductivity. If i augments, and U has tendency to the IR drop term, RI derived from Equation (28), which significates that electric power changes as RI2. Therefore, power input may be diminished upon reducing the gap among the plaques and augmenting the electrode surface area and the water conductivity [66]. Employing current reversal (switching anode and cathode electrically) is helpful to decrease maintenance price; however, its impact on contamination elimination is not ascertained until this moment.
Impact of the water pH
Besides the electric current, pH is an additional fundamental parameter touching the EC efficiency, specifically coagulating stages because it dictates the hydrolyzed metal species produced in reactive solution and affects the active steps of EC [82]. As shown in Section 2, investigating the Al and Fe speciation as a result from hydrolysis of their corresponding cations dictated upon thermodynamic equilibrium is crucial to explain the manner by which pH participates in imposing the stages of the electrochemical coagulation. There is no doubt that adsorption and coagulation are importantly depending on pH. The superficial charge of the Al or Fe flocs may be interpreted upon the adsorption of the charged soluble monomeric species on their respective hydroxide flocs [81]. The behavior among the pH-dependent coagulant species and their near contaminants may be determined from electrostatic interactions. Researchers such as Jiménez et al. [81] mentioned a detailed description taking into account these stages, i.e., double-layer compression, neutralization and sweep flocculation, for Al and Fe-EC intending to optimize the removal of several contaminants depending on the predominating hydrolyzed metal species. The significance of pH on EC efficiency may be at the same degree understood throughout the thermodynamics linked to the electrochemistry as described upon the Nernst equation. This relationship permits us showing the E-pH diagram of a useful electrode material that, once superimposed on E-pH diagram of water, conducts to a diagram well described as Pourbaix diagram. The Pourbaix diagram illustrates the areas of thermodynamically stable metal species in the aqueous medium, i.e., immunity, passivation, and corrosion, which lets to predict the corresponding electrode stability and its dissolution behavior in water throughout describing the stable aqueous species in a specific region of electrochemical potential and pH [5].
Researchers [51] examined the Al and Fe speciation intending to determine the predominance diagrams of corresponding hydroxides and to evaluate a fraction of undissolved hydroxides as a function of pH taking into account only monomeric species. For Al electrode, it has been established that the quantity of undissolved Al(OH)3 augments importantly with elevating pH from 4.5 to 7 to the detriment of aluminum hydroxide ions and the reverse is correct for a pH from 7 to 10; at the same time, amorphous metal hydroxide is not detected above the latter pH value. For the Fe electrode, the amount of undissolved iron hydroxide significantly augments with pH varying from 4 to 7 [93]. At pH 7, iron hydroxide ions are not present in the predominance diagram. These predominance diagrams were realized from the theoretical computation founded on equilibrium constants and pH for a concentration of 10-2 M for both electrode metals [5].
It should be mentioned that solution pH after EC operation would augment for acidic pH; however, it may diminish for alkaline pH, which is attributed to the buffering impact of EC [94]. The augmentation of pH in acidic water is explained by hydrogen production at the cathode; while the diminution of pH is linked firstly to the apparition of hydroxide precipitates that liberate H+ protons near the anode and the additional reactions like water oxidation and chlorine generation and its hydrolysis [95]. This fact focuses on the buffering impact of EC that enters in action in addition to that of water alkalinity [5]. This impact is significantly elevated with Al electrodes due to the generation of aluminate anions at elevated pH [39].
It was mentioned that the bicarbonate alkalinity ameliorates at a small degree the contaminants elimination performance [96]; moreover, it aids to reduce the hardness throughout precipitation of CaCO3 due to the hydroxyl anions formed upon water reduction near the cathode [5,46].
Impact of cell geometry and electrodes conception
The EC apparatus is mostly constituted of electrodes and enclosure. The electrodes are placed in a ring that is a non-conductive recipient in which the treatment of water happens [5].
- Electrodes arrangement: The electrode system primarily influences EC method through electrodes arrangement and inter-electrode gap. Electrodes arrangement may either be easily constituted of an anode and a cathode or be formed of several anodes and cathodes complicatedly arranged in EC tank. The complicated electrodes settlement may be categorized in monopolar and bipolar electrodes (Figure 5) [5]. Table 6 summarizes a description of the different configurations of the electrodes.
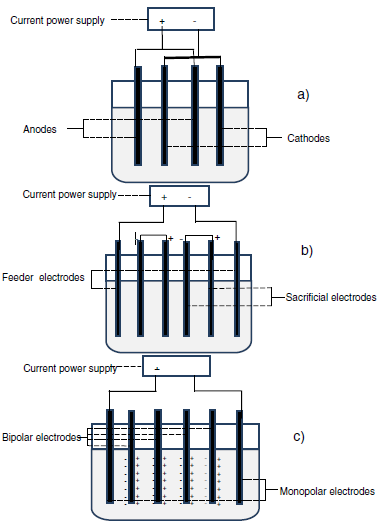
Figure 5: Monopolar electrodes: (a) in parallel connections, (b) in series connections; (c) bipolar electrodes in series connections [5].
|
Electrodes configuration
|
Description
|
Monopolar electrodes in parallel connection (MP-P)
|
MP-P are illustrated in Figure. 6a. The electrode settlement is composed of cathodes and anodes arranged alternatively at the same anodic or cathodic potential, respectively. Each pair of cathode/anode corresponds to a small electrolytic cell in which the voltage is the same. Thus, the reactor is composed of electrolytic cells in parallel. Therefore, the current of each electrolytic cell is additive.
|
Monopolar electrodes in series connections (MP-S)
|
MP-S are defined in Figure. 6b. Each pair of internal sacrificial electrodes is internally linked with each other and has no interconnections with the two outer electrodes. The electric current traveling through all the electrodes is the same, whereas the global voltage is the sum of tension in each electrolytic cell.
|
Bipolar electrodes in series connections (BP-S)
|
BP-S comprise two outer electrodes attached to the electric power supply and the sacrificial electrodes fixed among the two external electrodes (Figure. 6c). Outer electrodes are monopolar, and the inner ones are bipolar. The bipolar electrodes are not interconnected, and each of their sides acts simultaneously as an anode and a cathode. This fact implies that the opposite sides of each bipolar electrode are oppositely charged, the anodic dissolution happens on the positive side; at the same time, the negative side is prone to cathodic reactions [28].
|
Table 6: Various electrodes configurations used in EC process [5].
|
In a general manner, monopolar electrodes necessitate a low voltage and a more significant current contrary to the bipolar electrodes that work under high tension and a smaller current [5]. It is not easy to affirm which electrodes settlement is more significant than the other taking into account solely EC performance considering that it has been established that at the same level BP-S may show an elevated EC performance [97,98]. Monopolar electrodes can be viewed as significant because in several situations this electrodes arrangement provides an elevated contaminant reduction with a lower energy consumption [99,100], taking into account that bipolar electrode frequently consumes high energy [101-103]. The previous configuration is not difficult to manipulate and requires less maintenance cost throughout function; therefore, the effect of maintenance cost on global operation cost should at the same level be taken into account to select a convenient electrode configuration [37].
More than the typical rectangular electrodes, there are additional geometrical forms like circular and cylindrical. Electrodes may be placed either vertically or horizontally in EC cell [5]. Even if being scarcely employed, horizontal electrodes in EC batch reactor may possess a more significant mixing [104] performance [105].
- Inter-electrode gap: It is well-known that if the IR-drop augments, the difference among electrodes increases. This fact means that energy consumption diminishes with reducing the distance among the electrodes (Equations (27) and (28)) [5]. As the separation among the electrodes becomes lower, more electrochemically produced gas bubbles bring about turbulent hydrodynamics. This fact conducts to a high-mass transfer as well as to a high reaction rate amongst the coagulant species and contaminants [106]. Moreover, inter-electrode distance describes the contact period between the anode and the cathode for a continuous system and the period of operation for a batch reactor for attaining a wanted EC performance. For a complicated electrode placement, inter-electrode separation dictates as well the number of electrodes to arrange in EC cell, if its volume is fixed [107]. On the other hand, EC reactor conception is crucial because it influences the global efficiency of the EC method in the matter of its impact on the working variables, i.e., flow regime, flocs production, reduction percentage, and flotation/settling features [5,74].
An in-depth discussion of the EC reactor conception may be found in the excellent review of Hakizimana et al. [5].
Influence of water conductivity
The current density contribution is a function of conductivity and ionic strength of the solution. The current density effect augments if the electrolytic conductivity is elevated thanks to the reduction of the ohmic resistance of water. Moreover, the electric conductivity contributes to reducing the residence period needed to attain the desired reduction percentage [108]. As a result, energy consumption (UI) is decreased. Usually, NaCl is employed to augment the electrolytic conductivity. In addition, Cl- contributes to the decrease of the negative impacts of different anions to reduce the precipitation of calcium carbonate in hard water that may constitute an insulating film on the electrodes surface [94]. If the current density is elevated, Cl- may as well be oxidized to active chlorine forms, like hypochlorite anions, that may oxidize organic matters [37] and ferrous ions [5] or participate in killing microorganisms in water [109-112]. To providing an efficient function of EC in treating water, it is suggested that 20% of the anion’s existent must be Cl- [77].
Nevertheless, there are the limits dictated on conductivity augmentation in drinking water treatment [113]. Indeed, conductivity augmentation throughout the treatment of potable water using EC is significantly restricted in following the standard norms that describe the maximum chloride level in industrial effluents at 250 mg/L [5].
Influence of temperature
Temperature is an important parameter affecting EC process. Usually, EC process is realized at ambient temperature. During EC operation, the water temperature may increase due to the Joule effect. This phenomenon is more pronounced if the water conductivity is elevated especially in the case of brackish water or seawater treatment [49,109]. In this case, some precautions should be taken such as reducing the applied voltage and decreasing the residence time to avoid overheating of the electric components and circuit [80].
EC Modeling
At the best of our knowledge, the consulted references through this review proved the absence of an algorithmic and direct method of EC reactor conception. The significant enhancements in EC device efficiency and function require better design, materials, and optimization. These need a fundamental comprehension of the respective contributions of several phenomena implied in EC, comprising electrochemical mechanisms, coagulation, flotation, and settling [66]. EC modeling is importantly useful to enhance the conception and decrease equipment and operating costs simultaneously. It may easily ensure viable and correct solutions to EC issues, and therefore let us evaluate EC setup efficiency under a considerable interval of working situations [5].
Hakizimana et al. [5] discussed the EC models previously mentioned and examined in the specific references, and that may assist in reaching more comprehensions in EC devices conception. In a general manner, there are two principal categories of EC modeling: statistical modeling and modeling funded on knowledge. Mathematical modeling usually is destined to searching optimum working parameters in which EC performance will be enhanced. Since EC is a complicated method, modeling founded on knowledge embraces specific models that adopt EC as one method and some others that are employed to define a given physical or chemical process happening throughout the technique. Moreover, a particular focus is given to the Computational Fluid Dynamics (CFD) modeling; for which computational techniques have been used to investigate the fluid flow and current density inside EC devices and predict complicated inherent processes, particularly if technical restrictions limit an experimental method.
Table 7 summarizes the main features of the statistical modeling and modeling funded on knowledge of the EC process [5].
Modeling
|
Description
|
Statistical
modeling
|
Taking into account several physical/chemical processes implicated in EC, the contaminants elimination performance complicatedly is the function of the separated and additional impacts of the key technique parameters (factors). Until now, in the largest part of the investigations performed on water/wastewater treatment using EC, optimization has been reached through modifying a single parameter at the same time maintaining all remaining parameters set at a particular series of situations. This usual fashion for optimization of EC process needs several practice tests and conducts to a weak optimization, like underestimation or overestimation of the impact of the method factors on EC efficiencies because of neglecting the mutual contributions inside those parameters [114]. Response surface methodology (RSM) has been employed as a method in many studies to show the impacts of main process factors and their mutual contributions. RSM is used in multiple forms such as the full or partial factorial design (FD) [115,116], central composite design (CCD) [117-121], D-optimal design (DOP) [114], and Box-Behnken design (BBD) [122-125], etc.
|
Modeling
funded
on knowledge
|
- Phenomenological models
In several studies, EC kinetics has been investigated to model and simulate the EC process. Several researchers such as Mameri et al. [78] have tried to model EC kinetics of the removal of fluoride anions. Kinetics of defluoridation was shown to obey an exponential law with time so that it turned out to be first-order for fluoride concentration. Moreover, the elimination of contaminants like nitrates [54,126] and heavy metals by EC obeyed to an n-order kinetic model [127].
- Modeling detailed mechanisms
- Electrochemical phenomena
EC technique is mainly founded on electrochemistry since the electrochemical events are the initiating heart of the whole method. Electrochemistry is viewed as a complicated knowledge since it concerns at the same time charge transport, electrochemical kinetics, comprehension of electrodes interface and thermodynamics.
- Adsorption
To better assess the stages implicated in EC and for modeling aim, pure adsorption isotherm and adsorption kinetics models have mainly been employed. Because the quantity of coagulant formed may be evaluated for a specific period by applying Faraday's law, contamination reduction may be seen from the adsorption phenomenon point of view [128]. The most common adsorption isotherms employed for EC modeling founded on the hypothesis of thermodynamic monitoring are mainly the Langmuir and Freundlich isotherms and the Langmuir–Freundlich model that uses the two previous ones. The Langmuir isotherm supposes a monolayer deposition of the adsorbate on a homogenous adsorbent surface, while the Freundlich isotherm defines reversible adsorption that may be followed by multilayer formation [129].
- Flocculation modeling
Flocculation is a complicated method during which two or more colliding destabilized colloids adhere together and constitute a floc. Stages happening throughout flocculation may be summarized into two steps: transport conducting to the collision and fixation. The first one is realized through (a) Brownian motion of the colloids (perikinetic flocculation), (b) fluid motion (orthokinetic flocculation) and (c) differential settling velocities attributed to gravity. Fixation is a consequence of the interparticle forces [130].
- Flotation and settling
The formed flocs during EC may be eliminated upon various physical manners, as illustrated in Figure 4. EF appears thanks to buoyancy forces and settling thanks to gravity. EF is a function of current density, hydrogen micro-bubbles size (20-50 μm) and particle collection performance by the micro-bubbles [24]. Even if the current density imposes a convenient contaminant reduction mechanism, particularly in batch systems, it is not easy to entirely escape to either settling or EF in favor of the remaining stages, whatever the current density that may be employed.
- Complexation
Complexation model is a modern phenomenological model illustrating adsorption equilibrium that is imposed by complexation of suspended matter upon Fe or Al hydroxides for chemical oxygen demand removal.
|
Modeling utilizing CFD
|
Recently, like in several research domains, CFD simulations have reached a significant role to play in the comprehension and enhancement of the EC reactors design for the next future. Many authors have focused on different features of flows inside electrochemical cells [131-134]. CFD seems to be useful and exciting in comprehending the hydrodynamic and contact period distribution to describe the flow pattern and may be successfully used to predict the principal local characteristics of the method, such as velocity profiles, the reaction rate distribution at the electrodes and the cell voltage. CFD has been employed to examine the distribution of potential and current density because the latter shows the distribution of attack on electrode surface throughout its dissolution and may be helpful in the EC reactor conception for energy efficiency [131].
|
Table 7: EC process statistical modeling and modeling funded on knowledge [5].
|
Conclusions
From this review, the main points drawn are listed as below:
- Similar experiments, as jar test experiments used in conventional coagulation to determine the optimal coagulant doses, should be conceived using Zeta-meters to control the EC optimal residence time better and metal amount liberated. An empirical method would be suggested to facilitate a direct approach to calculate the EC optimal parameters following the (1) water main characteristics such as electric conductivity, pH, pollutants concentrations and the (2) EC device features like metal type, reactor geometry and batch/continuous mode.
- The scientific community specialized in the EC process is near to suggest empirical/theoretical models to present the EC technology as a viable green process. However, more great efforts remain to be accomplished.
- Technological software developers such as COMSOL™ Multiphysics are invited to insert the EC process in their electrochemistry module in their future versions to better commercialize this intensified technique and encourage its massive use through the world.
References
- Ghernaout D (2017) Environmental principles in the Holy Koran and the Sayings of the Prophet Muhammad. Am J Environ Prot 6: 75-79.
- Ghernaout D (2017) Water reuse (WR): The ultimate and vital solution for water supply issues. Intern J Sustain Develop Res 3: 36-46.
- Ghernaout D (2018) Increasing trends towards drinking water reclamation from treated wastewater. World J Appl Chem 3: 1-9.
- World Health Organization (WHO) (2012) Global Analysis and Assessment of Sanitation and Drinking-Water (GLAAS). 1-112.
- Hakizimana JN, Gourich B, Chafi M, Stiriba Y, Vial C, et al. (2017) Electrocoagulation process in water treatment: A review of electrocoagulation modeling approaches. Desalination 404: 1-21.
- Boucherit A, Moulay S, Ghernaout D, Al-Ghonamy, Ghernaout B, et al. (2015) New trends in disinfection by-products formation upon water treatment. J Res Develop Chem.
- Ghernaout D, Ghernaout B (2012) On the concept of the future drinking water treatment plant: Algae harvesting from the algal biomass for biodiesel production-A Review. Desalin Water Treat 49: 1-18.
- Ghernaout D, Badis A, Braikia G, Matâam N, Fekhar M, et al. (2017) Enhanced coagulation for algae removal in a typical Algeria water treatment plant. Environ Eng Manag J 16: 2303-2315.
- Ghernaout D (2013) The best available technology of water/wastewater treatment and seawater desalination: Simulation of the open sky seawater distillation. Green Sustain Chem 3: 68-88.
- Ghernaout D, Alshammari Y, Alghamdi A, Aichouni M, Touahmia M, et al. (2018) Water reuse: Extenuating membrane fouling in membrane processes. Intern J Environ Chem 2: 1-12.
- Ghernaout D, Moulay S, Ait Messaoudene N, Aichouni M, Naceur MW, et al. (2014) Coagulation and chlorination of NOM and algae in water treatment: A review. Intern J Environ Monit Analy 2: 23-34.
- Ghernaout D (2017) Water treatment chlorination: An updated mechanistic insight review. Chem Res J 2: 125-138.
- Ghernaout D (2018) Magnetic field generation in the water treatment perspectives: An overview. Int J Adv Appl Sci 5: 193-203.
- Ghernaout D, Ghernaout B, Naceur MW (2011) Embodying the chemical water treatment in the green chemistry – A review. Desalination 271: 1-10.
- Ghernaout D (2018) Electrocoagulation process: Achievements and green perspectives. Colloid Surface Sci 3: 1-5.
- Ghernaout D (2013) Advanced oxidation phenomena in electrocoagulation process: A myth or a reality?. Desalin Water Treat 51: 7536-7554.
- Ghernaout D (2017) The Holy Koran Revelation: Iron is a “sent down” metal. Am J Environ Prot 6: 101-104.
- Ghernaout D, Ghernaout B, Saiba A, Boucherit A, Kellil A (2009) Removal of humic acids by continuous electromagnetic treatment followed by electrocoagulation in batch using aluminium electrodes. Desalination 239: 295-308.
- Ghernaout D, Ghernaout B, Boucherit A (2008) Effect of pH on electrocoagulation of bentonite suspensions in batch using iron electrodes. J Disper Sci Technol 29: 1272-1275.
- Ghernaout D, Mariche A, Ghernaout B, Kellil A (2010) Electromagnetic treatment-bi-electrocoagulation of humic acid in continuous mode using response surface method for its optimization and application on two surface waters. Desalin Water Treat 22: 311-329.
- Emamjomeh MM, Sivakumar M (2009) Review of pollutants removed by electrocoagulation and electrocoagulation/flotation processes. J Environ Manag 90: 1663-1679.
- Kabda?h I, Arslan-Alaton I, Ölmez-Hanci T, Tünay O (2012) Electrocoagulation applications for industrial wastewater: a critical review. Environ Technol Rev 1: 2-45.
- Ghernaout D, Alshammari Y, Alghamdi A (2018) Improving energetically operational procedures in wastewater treatment plants. Int J Adv Appl Sci 5: 64-72.
- Holt PK, Barton GW, Mitchell CA (2005) The future for electrocoagulation as a localized water treatment technology. Chemosphere 59: 355-367.
- Ghernaout D, Simoussa A, Alghamdi A, Ghernaout B, Elboughdiri N. et al. (2018) Combining lime softening with alum coagulation for hard Ghrib dam water conventional treatment. Inter J Adv Appl Sci 5: 61-70.
- Djezzar S, Ghernaout D, Cherifi H, Alghamdi A, Ghernaout B, et al. (2018) Conventional, Enhanced, and Alkaline Coagulation for Hard Ghrib Dam (Algeria) Water. World J Appl Chem 3: 41-55.
- Ghernaout D, Al-Ghonamy, Irki S, Grini A, Naceur MW, et al. (2014) Decolourization of bromophenol blue by electrocoagulation process. Trends Chem Eng 15: 29-39.
- Mollah MY, Schennach R, Parga JR, Cocke DL (2001) Electrocoagulation (EC)-science and applications. J Hazard Mater B 84: 29-41.
- Ghernaout D, Al-Ghonamy AI, Boucherit A, Ghernaout B, Naceur MW, et al. (2015) Brownian motion and coagulation process. Am J Environ Prot 4: 1-15.
- Ghernaout D, Al-Ghonamy AI, Naceur MW, Boucherit A, Messaoudene NA, et al. (2015) Controlling coagulation process: From Zeta potential to streaming potential. Am J Environ Prot 4: 16-27.
- Ghernaout D, Laribi C, Alghamdi A, Ghernaout B, Ait N, et al. (2018) Decolorization of BF Cibacete Blue (CB) and Red Solophenyle 3BL (RS) using aluminum sulfate and ferric chloride. World J Appl Chem 3: 32-40.
- Ghernaout D, Al-Ghonamy AI, Ait Messaoudene N, Aichouni M, Naceur MW et al. (2015) Electrocoagulation of Direct Brown 2 (DB) and BF Cibacete Blue (CB) using aluminum electrodes. Sep Sci Technol 50: 1413-1420.
- Ghernaout D, Alghamdi A, Touahmia M, Aichouni M, Ait Messaoudene N (2018) Nanotechnology phenomena in the light of the solar energy. J Energ Environ Chem Eng 3: 1-8.
- Ghernaout D, Ghernaout B, Boucherit A, Naceur MW, Khelifa A, et al (2009) Study on mechanism of electrocoagulation with iron electrodes in idealised conditions and electrocoagulation of humic acids solution in batch using aluminium electrodes. Desalin Water Treat 8: 91-99.
- Saiba A, Kourdali S, Ghernaout B, Ghernaout D (2010) In Desalination, from 1987 to 2009, the birth of a new seawater pretreatment process: Electrocoagulation-an overview. Desalin Water Treat 16: 201-217.
- Holt, Pater Kevin (2002) Electrocoagulation: Unraveling and synthesizing the mechanisms behind a water treatment process. The University of Sydney
- Kobya M, Can OT, Bayramoglu M (2003) Treatment of textile wastewaters by electrocoagulation using iron and aluminum electrodes. J Hazard Mater 100: 163-178.
- Mouedhen G, Feki M, De Petris Wery M, Ayedi HF (2008) Behavior of aluminum electrodes in electrocoagulation process. J Hazard Mater 150: 124-135.
- Chen X, Chen G, Yue PL (2000) Separation of pollutants from restaurant wastewater by electrocoagulation. Sep Purif Technol 19: 65-76.
- Den W, Wan CJ (2008) Removal of silica from brackish water by electrocoagulation pretreatment to prevent fouling of reverse osmosis membranes. Sep Purif Technol 59: 318-325.
- Hu CY, Lo SL, Kuan WH (2007) Simulation the kinetics of fluoride removal by electrocoagulation (EC) process using aluminum electrodes. J Hazard Mater 145: 180-185.
- Bagga A, Chellam S, Clifford DA (2008) Evaluation of iron chemical coagulation and electrocoagulation pretreatment for surface water microfiltration. J Membr Sci 309: 82-93.
- Gu Z, Liao Z, Schulz M, Davis JR, Baygents JC, et al. (2009) Estimating dosing rates and energy consumption for electrocoagulation using iron and aluminum electrodes. Ind Eng Chem Res 48: 3112-3117.
- Mansouri K, Ibrik K, Bensalah N, Abdel-Wahab A (2011) Anodic dissolution of pure aluminum during electrocoagulation process: influence of supporting electrolyte, initial pH, and current density. Ind Eng Chem Res 50: 13362-13372.
- Vepsäläinen M, Selin J, Rantala P, Pulliainen M, Särkkä H, et al (2011) Precipitation of dissolved sulphide in pulp and paper mill wastewater by electrocoagulation. Environ Technol 32: 1393-1400.
- De Mello Ferreira A, Marchesiello M, Thivel P-X (2013) Removal of copper, zinc and nickel present in natural water containing Ca2+ and HCO3- ions by electrocoagulation. Sep Purif Technol 107: 109-117.
- Lacasa E, Canizares P, Sáez C, Fernández FJ, Rodrigo MA (2011) Electrochemical phosphates removal using iron and aluminium electrodes. Chem Eng J 172: 137-143.
- Golder AK, Samanta AN, Ray S (2006) Removal of phosphate from aqueous solutions using calcined metal hydroxides sludge waste generated from electrocoagulation. Sep Purif Technol 52: 102-109.
- Ghernaout D, Ghernaout B, Kellil A (2009) Natural organic matter removal and enhanced coagulation as a link between coagulation and electrocoagulation. Desalin Water Treat 2: 203-222.
- Ghernaout D (2014) The hydrophilic/hydrophobic ratio vs. dissolved organics removal by coagulation - A review. J King Saud Univ – Sci 26: 169-180.
- Emamjomeh MM, Sivakumar M, Varyani (2011) AS Analysis and the understanding of fluoride removal mechanisms by an electrocoagulation/flotation (ECF) process. Desalination 275: 102-106.
- Hu CY, Lo SL, Kuan WH (2014) High concentration of arsenate removal by electrocoagulation with calcium. Sep Purif Technol 126: 7-14.
- Zongo I, Leclerc JP, Maiga HA, Wéthé J, Lapicque F (2009) Removal of hexavalent chromium from industrial wastewater by electrocoagulation: a comprehensive comparison of aluminium and iron electrodes. Sep Purif Technol 66: 159-166.
- Emamjomeh MM, Sivakumar M (2009) Denitrification using a monopolar electrocoagulation/flotation (ECF) process. J Environ Manag 91: 516-522.
- Kumar PR, Chaudhari S, Khilar KC, Mahajan SP (2004) Removal of arsenic from water by electrocoagulation. Chemosphere 55: 1245-1252.
- Al Aji B, Yavuz Y, Koparal AS (2012) Electrocoagulation of heavy metals containing model wastewater using monopolar iron electrodes. Sep Purif Technol 86: 248-254.
- Ghernaout D, Irki S, Boucherit A (2014) Removal of Cu2+ and Cd2+, and humic acid and phenol by electrocoagulation using iron electrodes. Desalin Water Treat 52: 3256-3270.
- Zhu J, Zhao H, Ni J (2007) Fluoride distribution in electrocoagulation defluoridation process. Sep Purif Technol 56: 184-191.
- Hu CY, Loa SL, Kuan WH (2003) Effects of co-existing anions on fluoride removal in electrocoagulation (EC) process using aluminum electrodes. Water Res. 37: 4513-4523.
- Duan J, Gregory J (2003) Coagulation by hydrolyzing metal salts. Adv Colloid Interf Sci 100-102: 475-502.
- B Derjaguin, L Landau (1941) Theory of the stability of strongly charged lyophobic sols and of the adhesion of strongly charged particles in solutions of electrolytes. Acta Phys Chim 14: 633-662.
- Verwey EJW, Overbeek JThG (1948) Theory of the stability of lyophobic colloids. Elsevier. Amsterdam, London.
- Liang Y, Hilal N, Langston P, Starov V (2007) Interaction forces between colloidal particles in liquid: theory and experiment. Adv Colloid Interf Sci 134-135: 151-166.
- Cañizares P, Martínez F, Rodrigo MA, Jiménez C, Sáez C, et al. (2008) Modeling of wastewater electrocoagulation processes part I. General description and application to kaolin-polluted wastewaters. Sep Purif Technol 60: 155-161.
- Ghernaout D, Ghernaout B (2012) Sweep flocculation as a second form of charge neutralisation – A review. Desalin Water Treat 44: 15-28.
- Mollah MY, Morkovsky P, Gomes JA, Kesmez M, Parga J, et al. (2004) Fundamentals, present and future perspectives of electrocoagulation. J Hazard Mater B114: 199-210.
- Ghernaout B, Ghernaout D, Saiba A (2010) Algae and cyanotoxins removal by coagulation/flocculation: A review. Desalin Water Treat 20: 133-143.
- Ghernaout D, Naceur MW, Ghernaout B (2011) A review of electrocoagulation as a promising coagulation process for improved organic and inorganic matters removal by electrophoresis and electroflotation. Desalin Water Treat 28: 287-320.
- Ghernaout D, Benblidia C, Khemici F (2015) Microalgae removal from Ghrib Dam (Ain Defla, Algeria) water by electroflotation using stainless steel electrodes. Desalin Water Treat 54: 3328-3337.
- Bayramoglu M, Kobya M, Can OT, Sozbir M (2004) Operating cost analysis of electrocoagulation of textile dye wastewater. Sep Purif Technol 37: 117-125.
- Can OT, Bayramoglu M, Kobya M (2003) Decolorization of reactive dye solutions by electrocoagulation using aluminum electrodes. Ind Eng Chem Res 42: 3391-3396.
- Kobya M, Hiz H, Senturk E, Aydiner C, Demirbas E (2006) Treatment of potato chips manufacturing wastewater by electrocoagulation. Desalination 190: 201-211.
- Ghernaout D, Al-Ghonamy AI, Naceur MW, Ait Messaoudene N, Aichouni M (2014) Influence of operating parameters on electrocoagulation of C.I. disperse yellow 3. J Electrochem Sci Eng 4: 271-283.
- Hansen HK, Nuñez P, Raboy D, Schippacasse I, Grandon R (2007) Electrocoagulation in wastewater containing arsenic: comparing different process designs. Electrochim. Acta 52: 3464-3470.
- Mansouri K, Elsaid K, Bedoui A, Bensalaha N, Abdel-Wahab A (2011) Application of electrochemically dissolved iron in the removal of tannic acid from water. Chem Eng J 172: 970-976.
- Ghernaout D, Ghernaout B (2011) On the controversial effect of sodium sulphate as supporting electrolyte on electrocoagulation process: A review. Desalin Water Treat 27: 243-254.
- Comninellis C, Chen G (2010) Electrochemistry for the Environment, Springer Science + Business Media. LLC
- Mameri N, Yeddou AR, Lounici H, Belhocine D, Grid H, et al. (1998) Defluoridation of septentrional Sahara water of North Africa by electrocoagulation process using bipolar aluminium electrodes. Water Res. 32: 1604-1612.
- Ghernaout D, Naceur MW (2011) Ferrate(VI): In situ generation and water treatment – A review. Desalin Water Treat 30: 319-332.
- Irki S, Ghernaout D, Naceur MW, Alghamdi A, Aichouni M (2018) Decolorization of methyl orange (MO) by electrocoagulation (EC) using iron electrodes under a magnetic field (MF). II. Effect of connection mode. World J Appl Chem 3: 56-64.
- Jiménez C, Sáez C, Martínez F, Cañizares P, Rodrigo MA (2012) Electrochemical dosing of iron and aluminum in continuous processes: a key step to explain electro-coagulation processes. Sep. Purif. Technol. 98: 102-108.
- Malakootian M, Mansoorian HJ, Moosazadeh M (2010) Performance evaluation of electrocoagulation process using iron-rod electrodes for removing hardness from drinking water. Desalination 255: 67-71.
- Irki S, Ghernaout D, Naceur MW, Alghamdi A, Aichouni M (2018) Decolorizing Methyl Orange by Fe-Electrocoagulation Process – A Mechanistic Insight. Inter J Environ Chem 2: 18-28.
- Lakshmanan D, Clifford DA, Samanta G (2009) Ferrous and ferric ion generation during iron electrocoagulation. nviron Sci Technol 43: 3853-3859.
- Akyol A (2012) Treatment of paint manufacturing wastewater by electrocoagulation. Desalination 285: 91-99.
- Kobya M, Senturk E, Bayramoglu M (2006) Treatment of poultry slaughterhouse wastewaters by electrocoagulation. J Hazard Mater 133: 172-176.
- Chafi M, Gourich B, Essadki AH, Vial C, Fabregat A (2011) Comparison of electrocoagulation using iron and aluminium electrodes with chemical coagulation for the removal of a highly soluble acid dye. Desalination 281: 285-292.
- Holt PK, Barton GW, Wark M, Mitchell CA (2002) A quantitative comparison between chemical dosing and electrocoagulation. Colloids Surf A Physicochem Eng Asp 211: 233-248.
- Ghernaout D, Badis A, Ghernaout B, Kellil A (2008) Application of electrocoagulation in Escherichia Coli culture and two surface waters. Desalination 219: 118-125.
- Koparal AS, Ögütveren ÜB (2002) Removal of nitrate from water by electroreduction and electrocoagulation. J Hazard Mater B89: 83-94.
- Fan L, Zhou Y, Yang W, Chen G, Yang F (2008) Electrochemical degradation of aqueous solution of Amaranth azo dye on ACF under potentiostatic model. Dyes Pigments 76: 440-446.
- Ruotolo LAM, Gubulin JC (2011) A mathematical model to predict the electrode potential profile inside a polyaniline-modified reticulate vitreous carbon electrode operating in the potentiostatic reduction of Cr(VI). Chem Eng J 171: 1170-1177.
- Irki S, Ghernaout D, Naceur MW (2017) Decolourization of Methyl Orange (MO) by Electrocoagulation (EC) using iron electrodes under a magnetic field (MF). Desalin Water Treat 79: 368-377.
- Chen G (2004) Electrochemical technologies in wastewater treatment. Sep Purif Technol 38: 11-41.
- Ghernaout D, Naceur MW, Aouabed A (2011) On the dependence of chlorine by-products generated species formation of the electrode material and applied charge during electrochemical water treatment. Desalination 270: 9-22.
- Zhao HZ, Yang W, Zhu J, Ni JR (2009) Defluoridation of drinking water by combined electrocoagulation: effects of the molar ratio of alkalinity and fluoride to Al (III). Chemosphere 74: 1391-1395.
- Bayramoglu M, Eyvaz M, Kobya M (2007) Treatment of the textile wastewater by electrocoagulation: economical evaluation. Chem Eng J 128: 155-161.
- Golder AK, Samanta AN, Ray S (2007) Removal of Cr3+ by electrocoagulation with multiple electrodes: bipolar and monopolar configurations. J Hazard Mater 141: 653-661.
- Kobya M, Ulu F, Gebologlu U, Demirbas E, Oncel MS (2011) Treatment of potable water containing low concentration of arsenic with electrocoagulation: different connections mode and Fe-Al electrodes. Sep Purif Technol 77: 283-293.
- Wang CT, Chou WL, Kuo YM (2009) Removal of COD from laundry wastewater by electrocoagulation/electroflotation. J Hazard Mater 164: 81-86.
- Drogui P, Asselin M, Brar SK, Benmoussa H, Blais (2008) JF Electrochemical removal of pollutants from agro-industry wastewaters. Sep Purif Technol 61: 301-310.
- Jiang JQ, Graham N, André C, Kelsall GH, Nigel B (2002) Laboratory study of electro-coagulation-flotation for water treatment. Water Res 36: 4064-4078.
- Modirshahla N, Behnajady MA, Kooshaiian S (2007) Investigation of the effect of different electrode connections on the removal efficiency of Tartrazine from aqueous solutions by electrocoagulation. Dyes Pigments 74: 249-257.
- Ghernaout D, Boucherit A (2015) Review of coagulation’s rapid mixing for NOM removal. J Res Develop Chem
- Fouad YOA, Konsowa AH, Farag HA, Sedahmed GH (2009) Performance of an electrocoagulation cell with horizontally oriented electrodes in oil separation compared to a cell with vertical electrodes. Chem Eng J 145: 436-440.
- Martínez-Villafañe JF, Montero-Ocampo C, García-Lara AM (2009) Energy and electrode consumption analysis of electrocoagulation for the removal of arsenic from underground water. J Hazard Mater 172: 1617-1622.
- Zhang S, Zhang J, Wang W, Li F Cheng X (2013) Removal of phosphate from landscape water using an electrocoagulation process powered directly by photovoltaic solar modules. Sol Energy Mater Sol Cells 117: 73-80.
- Chou WL (2010) Removal and adsorption characteristics of polyvinyl alcohol from aqueous solutions using electrocoagulation. J Hazard Mater 177: 842-850.
- Ghernaout D, Ghernaout B (2010) From chemical disinfection to electrodisinfection: The obligatory itinerary? Desalin Water Treat 16: 156-175.
- Belhout D, Ghernaout D, Djezzar-Douakh S, Kellil A (2010) Electrocoagulation of Ghrib dam’s water (Algeria) in batch using iron electrodes. Desalin. Water Treat. 16: 1-9.
- Ghernaout D (2017) Microorganisms’ electrochemical disinfection phenomena. EC Microbiol 9: 160-169.
- Ghernaout D (2018) Disinfection and DBPs removal in drinking water treatment: A perspective for a green technology. Int J Adv Appl Sci 5: 108-117.
- Ghernaout D, Aichouni M, Alghamdi A (2018) Applying Big Data (BD) in water treatment industry: A new era of advance. Int J Adv Appl Sci 5: 89-97.
- Tir M, Moulai-Mostefa N (2008) Optimization of oil removal from oily wastewater by electrocoagulation using response surface method. J Hazard Mater 158: 107-115.
- Chen W-J, Su W-T, Hsu H-Y (2012) Continuous flow electrocoagulation for MSG wastewater treatment using polymer coagulants via mixture-process design and response-surface methods. J Taiwan Inst Chem Eng 43: 246-255.
- Daghrir R, Drogui P, Zaviska F (2013) Effectiveness of a hybrid process combining electro-coagulation and electro-oxidation for the treatment of domestic wastewaters using response surface methodology. J Environ Sci Health A 48: 308-318.
- Garg KK, Prasad B (2016) Treatment of multicomponent aqueous solution of purified terephthalic acid wastewater by electrocoagulation process: optimization of process and analysis of sludge. J Taiwan Inst Chem Eng 60: 383-393.
- Amani-Ghadim AR, Aber S, Olad A, Ashassi-Sorkhabi H (2013) Optimization of electrocoagulation process for removal of an azo dye using response surface methodology and investigation on the occurrence of destructive side reactions. Chem Eng Process 64: 68-78.
- Gengec E, Kobya M, Demirbas E, Akyol A, Oktor K (2012) Optimization of baker's yeast wastewater using response surface methodology by electrocoagulation desalination. Water Air Soil Pollut 286: 200-209.
- Olmez-Hanci T, Kartal Z, Arslan-Alaton I (2012) Electrocoagulation of commercial naphthalene sulfonates: process optimization and assessment of implementation potential. J Environ Manag 99: 44-51.
- Bhatti MS, Reddy AS, Thukral AK (2009) Electrocoagulation removal of Cr(VI) from simulated wastewater using response surface methodology. J Hazard Mater 172: 839-846.
- Chavalparit O, Ongwandee M (2009) Optimizing electrocoagulation process for the treatment of biodiesel wastewater using response surface methodology. J Environ Sci 21: 1491-1496.
- Zodi S, Potier O, Lapicque F Leclerc J-P (2010) Treatment of the industrial wastewaters by electrocoagulation: optimization of coupled electrochemical and sedimentation processes. Desalination 261: 186-190.
- Garg KK, Prasad B (2016) Development of box Behnken design for treatment of terephthalic acid wastewater by electrocoagulation process: optimization of process and analysis of sludge. J Environ Chem Eng 4: 178-190.
- Tak B-Y, Tak B-S, Kim Y-J, Park Y-J, Yoon Y-H et al. (2015) Optimization of color and COD removal from livestock wastewater by electrocoagulation process: application of box–Behnken design (BBD). J Ind Eng Chem 28: 307-315.
- Yehya T, Chafi M, Balla W, Vial C, Essadki A et al. (2014) Experimental analysis and modeling of denitrification using electrocoagulation process. Sep Purif Technol 132: 644-654.
- Shafaei A, Pajootan E, Nikazar M, Arami M (2011) Removal of Co (II) from aqueous solution by electrocoagulation process using aluminum electrodes. Desalination 279: 121-126.
- Balasubramanian N, Kojima T, Srinivasakannan C (2009) Arsenic removal through electrocoagulation: kinetic and statistical modeling. Chem Eng J 155: 76-82.
- Chou WL, Wang CT, Chang WC, Chang SY (2010) Adsorption treatment of oxide chemical mechanical polishing wastewater from a semiconductor manufacturing plant by electrocoagulation. J Hazard Mater 180: 217-224.
- Ghernaout D (2017) Entropy in the Brownian motion (BM) and coagulation background. Colloid Surface Sci 2: 143-161.
- Vázquez A, Rodríguez I, Lázaro I (2012) Primary potential and current density distribution analysis: a first approach for designing electrocoagulation reactors. Chem Eng J 179: 253-261.
- Delgadillo SM, Ponce HM, Escamilla VM, Torres CG, Bernal JJ, et al. (2012) Performance evaluation of an electrochemical reactor used to reduce Cr(VI) from aqueous media applying CFD simulations. J Clean Prod 34: 120-124.
- Hashim KS, Al Khaddar R, Jasim N, Shaw A, Phipps D et al. (2019) Electrocoagulation as a green technology for phosphate removal from River water. Sep Purif Technol 210: 135-144.
- Hashim KS, Shaw A, Al Khaddar R, Pedrola MO, Phipps D (2017) Energy efficient electrocoagulation using a new flow column reactor to remove nitrate from drinking water - Experimental, statistical, and economic approach. J Environ Manage 196: 224-233.